ウォータージェット加工できる材料、注意点や設備導入のメリットについて
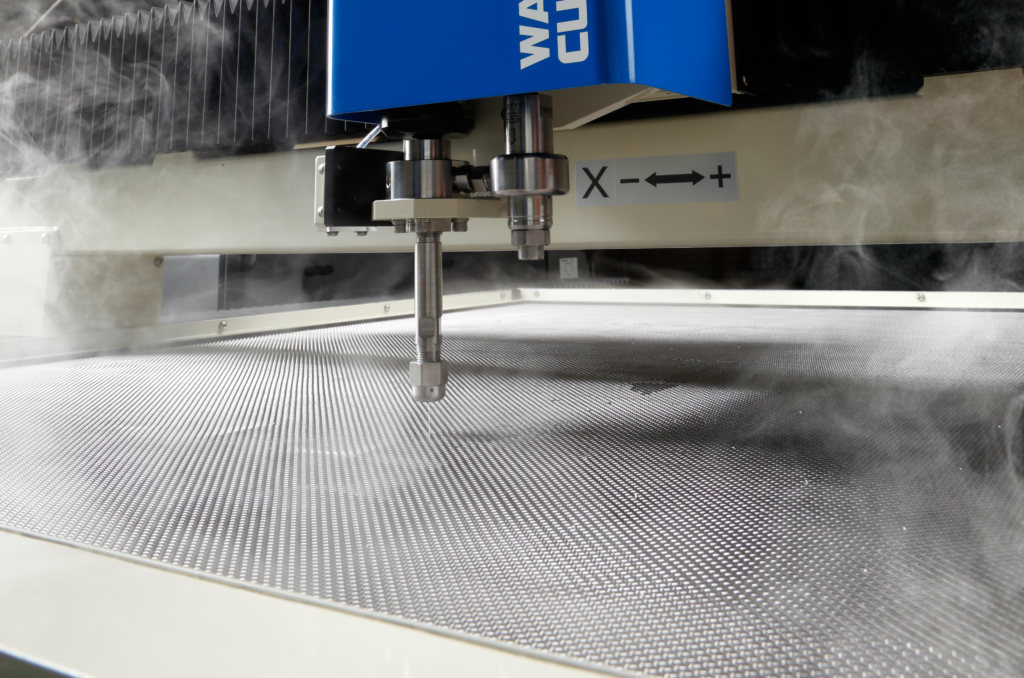
ウォータージェット加工は、超高圧の水流を利用した切断技術です。
本記事では、ウォータージェット加工で切断可能な材料や導入時の注意点、設備導入のメリットについて詳しく解説します。
キタガワのウォーターカッターについて
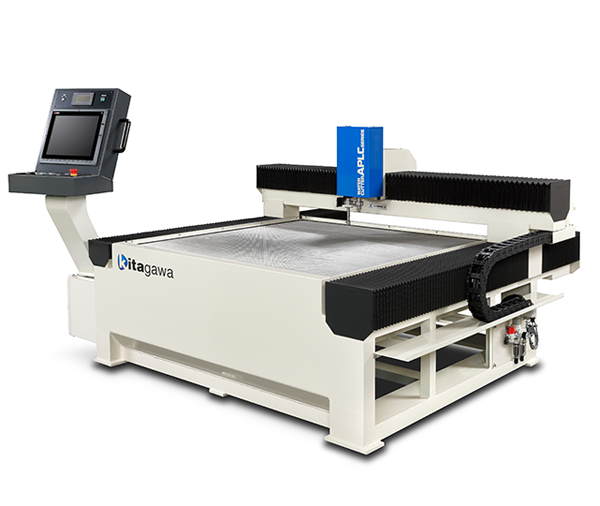
低価格モデル
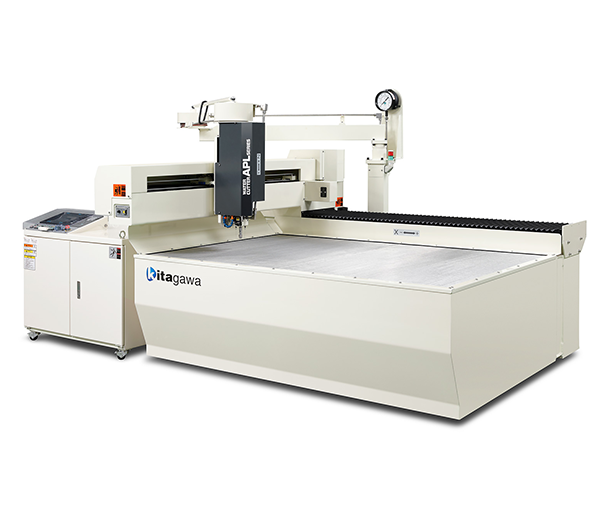
2軸制御ウォーターカッター
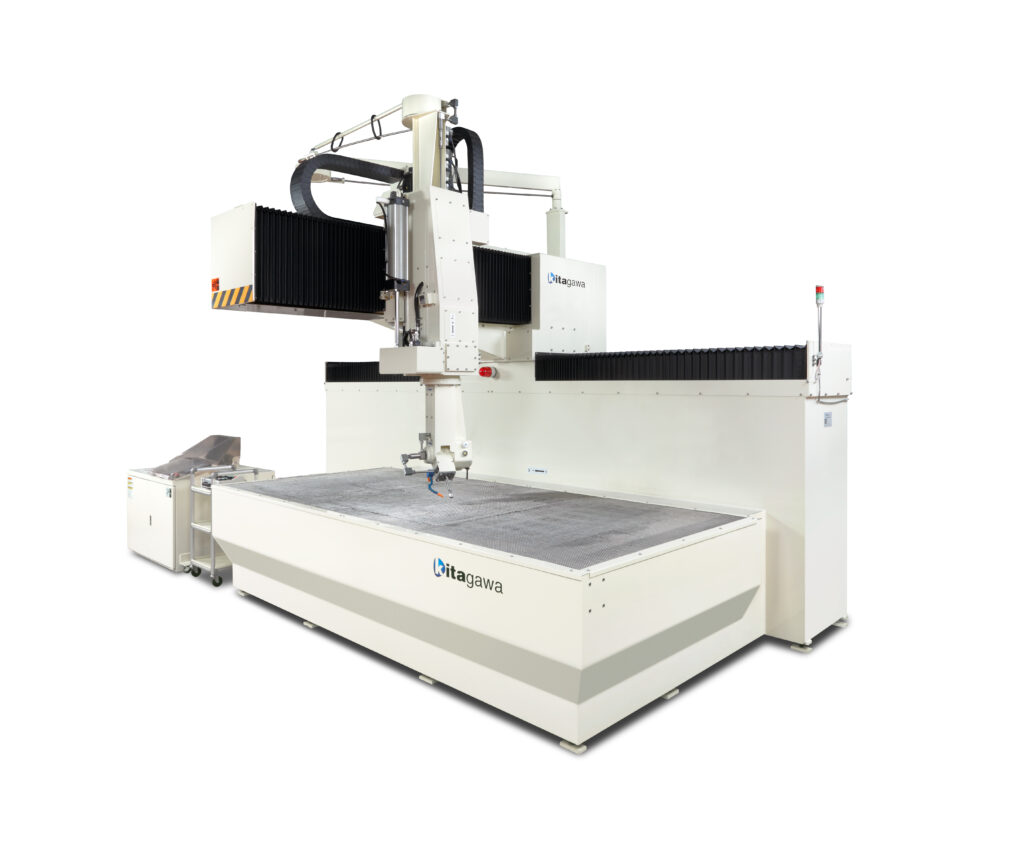
5軸制御ウォーターカッター
北川鉄工所は、多様なニーズに応える幅広いウォーターカッターのラインナップを取り揃えています。⽣産性向上に役⽴つ便利なオプション機能も充実。
導入後も安心してご使用いただけるよう、充実した操作トレーニングやメンテナンス、アフターフォローなどのサポート体制を整えています。
ウォータージェット加工とは
ウォータージェット加工は、超高圧の水流を利用して材料を切断・加工する技術です。約400MPa(水道水の約2700倍)もの超高圧水を、音速の約3倍の速度で小径ノズルから噴射することで、材料を切断します。この加工方法は、「ウォーターカッター」とも呼ばれ、どちらの呼び方も一般的に使用されています。
ウォータージェット加工には、水流のみを使用する「ピュアウォータージェット」と、水流に研磨材を混ぜて切断力を高めた「アブレイシブウォータージェット」の2種類があります。
北川鉄工所の装置は5軸加工機能を搭載し、立体的な切断や傾斜切断など、より複雑な加工にも対応できます。
ウォータージェット加工で切れる材料
ウォータージェット加工はその高い切断能力で様々な素材に対応し、金属、非金属を問わず幅広い材料加工を可能にします。
切れる材料一覧
ウォータージェットは、柔らかい材質から固い材質まで幅広く対応できます。
ウォータージェットで切れるもの | |||||
布地 | 石膏ボード | ウレタン | 鉄 | ガラス | アクリル |
ファブリック | 石綿 | ケブラー | ステンレス | カーボン | 花崗岩 |
皮 | グラスウール | グリーンセラミック | アルミニウム | ケブラー | 大理石 |
カーペット | FRP | ハードボード | チタン | グラファイト | |
ゴム | ポリ塩化ビニル | カーボンシート | 銅 | ファイバーグラス |
他の切断技術との比較
多くの切断技術は高温で材料を溶かしたり、工具で切断したりするため、熱影響が避けられません。一方、ウォータージェットは水を利用して切断するため、熱による変質、歪み、溶解が発生しにくく、精密な加工が可能です。
レーザーカッターやプラズマカッターなど多くの切断技術は、主に金属や一部の非金属に限定されます。一方、ウォータージェットは、その汎用性の高さも特徴の一つです。他の加工方法では対応困難な、複雑な形状にも対応できます。
レーザーカッターも高い精度を持ちますが、ウォータージェットは切断時の力が小さく、加工をする際に歪みを最小限に抑えることができます。
また、多くの切断技術は加工時に粉じんや有毒ガスが発生しますが、ウォータージェットは有毒ガスが発生しません。加工時の粉じんは水と一緒に流れるため飛散せず、クリーンな環境を維持できます。
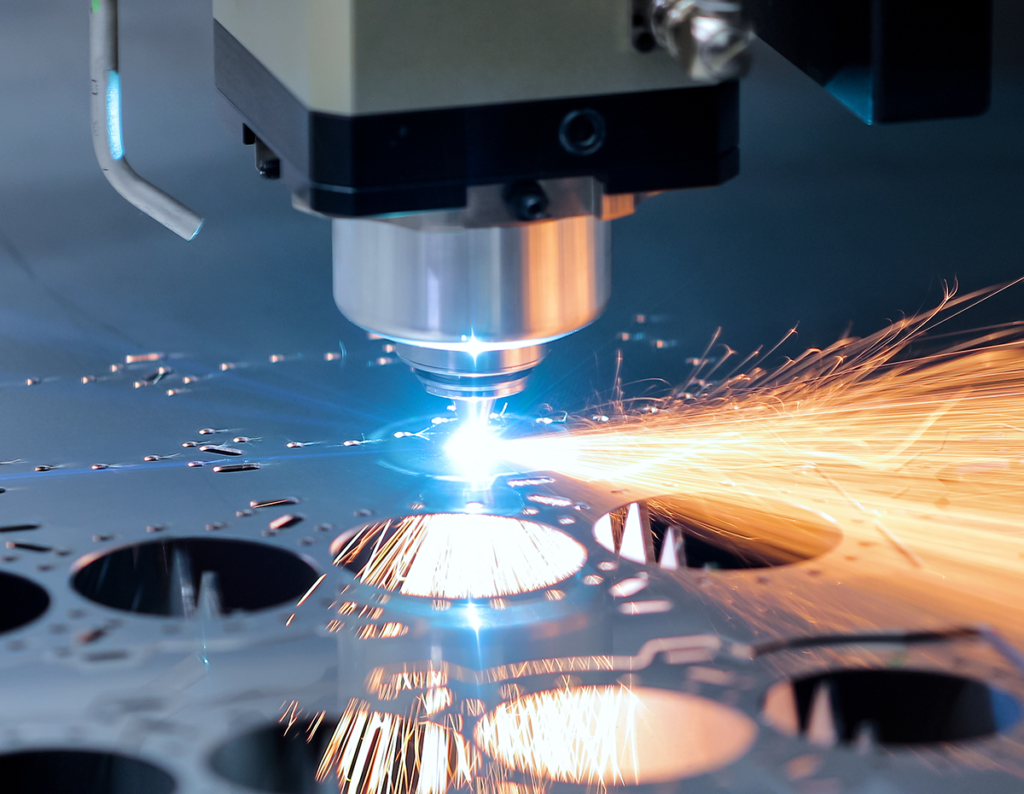
ウォータージェット加工のメリット
ウォータージェット加工には、多くの優れた特長があります。
まず、水流のみで切断を行うため、材料に熱影響を与えることがありません。材料の変形や変質を防ぎ、高精度な加工ができます。
また、金属、ガラス、石材、プラスチックなど、あらゆる素材に対応できる汎用性の高さも大きな特徴です。従来の加工方法では対応が難しかった材料でも、加工できます。
環境面でも優れており、加工時に有毒ガスの発生がなく、粉じんも水とともに回収されるため、クリーンな作業環境を維持できます。集塵装置などの付帯設備が不要な場合もあり、設備投資の削減にもつながります。
さらに、5軸加工機能を活用することで、立体的な切断や傾斜切断など、複雑な形状の加工にも対応可能です。
ウォータージェット加工のデメリットと注意点
ウォータージェット加工にはいくつかの制限や注意点があります。
レーザー加工と比較すると、一般的に加工速度が遅く、特に厚い材料や硬度の高い素材を加工する際は、さらに速度が低下します。
また、材料の厚さや硬度によって切断可能な範囲が制限されます。超硬合金のような極めて硬い素材は、400MPaの水圧でも切断が困難な場合があります。
ランニングコストも注意が必要です。水の使用量に加え、アブレイシブ加工時には研磨材の継続的な補充が必要となり、これらのコストは無視できません。
装置の操作やメンテナンスには、専門的な知識とスキルが必要です。ノズルやポンプなどの消耗品は定期的な交換が必要で、適切なメンテナンスを怠ると加工精度の低下や装置の故障につながる可能性があります。
さらに、特定の素材の加工は注意が必要です。例えば、薄板ガラスは水流の衝撃で割れやすく問題が発生することがあります。また、水を嫌う素材や吸水性の高い材料は、加工後の品質に影響が出る可能性があります。
ウォータージェット加工設備の導入メリット
ウォータージェット加工設備の導入は、製造現場に多くのメリットをもたらします。
加工できる材料の幅が広がる
金属、非金属を問わず、幅広い素材に対応できるため、一台の設備で複数の加工機の役割を担うことが可能です。熱の影響を受けやすい材料でも安全に加工でき、厚物から薄物まで、多様な板厚に対応できます。
ゴム
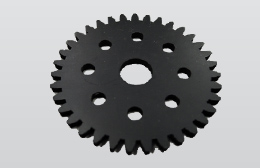
ジョイントシート
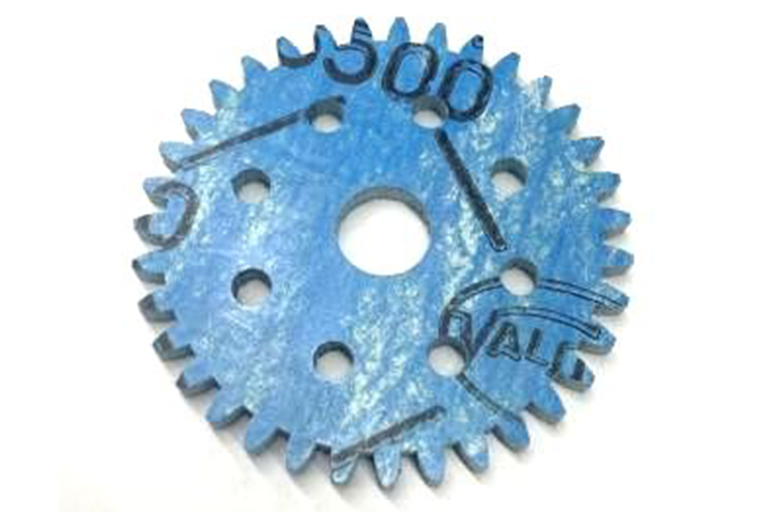
発泡体
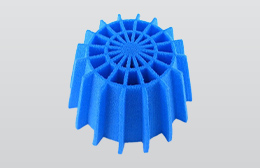
ウレタン

自動化とプログラム制御による効率化
CAD/CAMを用いた簡単なプログラミングで誰でも簡単に操作できます。複雑な形状も正確に再現可能。
金型不要で多品種少量生産に適した柔軟な生産体制を構築できます。無人運転による生産性向上も期待できます。
材料の歩留まり改善による資源の有効活用にもつながり、コスト削減と環境負荷低減の両立に貢献します。
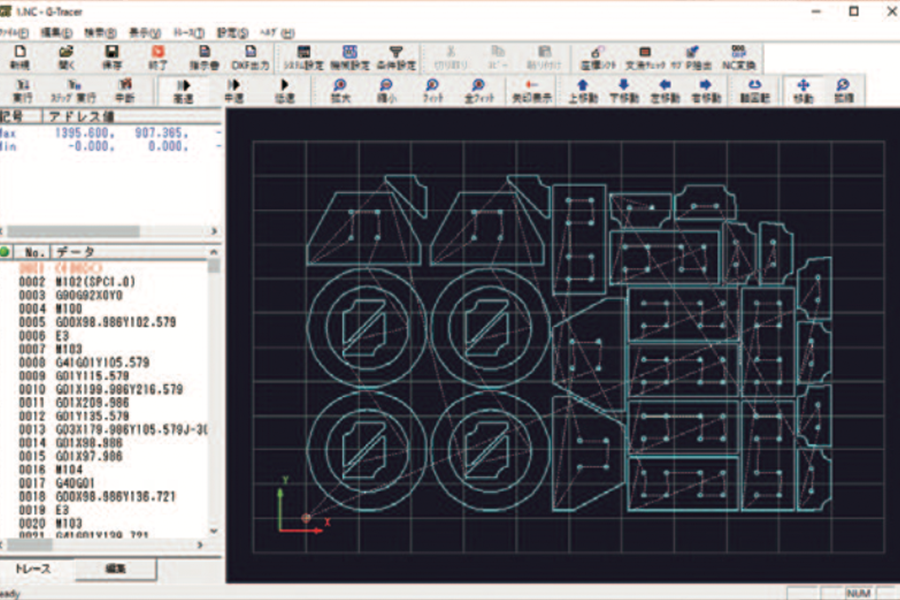
環境に優しい加工技術としての評価
有害ガスの発生がなく、作業環境が大幅に改善されます。水と研磨材のみを使用する加工方法であるため、環境負荷が少ないのも特徴です。粉じんの飛散も少なく、集塵設備が不要。騒音も比較的少なく、作業環境の改善が期待できます。さらに、材料のリサイクルが容易になる点も、環境への配慮という観点から重要なメリットと言えるでしょう。
ウォータージェット加工設備導入のコスト
ウォータージェット加工設備の導入には、初期投資とランニングコストの両面で検討が必要です。
初期投資と運用コストの見積もり
初期投資には、本体設備費用の他、以下の費用が必要となります。
- 設置工事費(基礎工事、電気工事、配管工事)
- 水処理設備
- 周辺機器(材料搬送装置、制御装置など)
- 操作トレーニング費用
ランニングコスト(電気、水、研磨剤)
ランニングコストの主な内訳は以下のとおりです。
- 電気代(超高圧ポンプの動力費)
- 水道代(切断用の水、冷却水)
- 研磨材費(アブレイシブ加工時)
- 消耗品費(ノズル、高圧シール、各種パッキンなど)
- メンテナンス費用(定期点検、部品交換)
ウォータージェット加工設備導入時の注意点
ウォータージェット加工設備を導入する際は、以下の点に注意が必要です。
設置スペースと設備要件
ウォータージェット加工設備は、超高圧ポンプや水処理装置など、周辺機器を含めると比較的大きな設置スペースが必要です。設置場所の広さだけでなく、床の耐荷重、電源容量、給排水設備、メンテナンススペースなども事前に確認しておく必要があります。
操作スタッフのトレーニングと技術習得
ウォータージェット加工機を最大限に活用するためには、操作スタッフの適切なトレーニングが不可欠です。単に機械の操作方法を覚えるだけでなく、CAD/CAMシステムの操作スキル、加工条件の設定や最適化のノウハウ、安全管理や緊急時の対応方法などの知識や技術を習得する必要があります
定期的なメンテナンスの重要性
ウォータージェット加工機は、高圧水流や研磨材を使用するため、消耗品の摩耗や機器の劣化が進みやすいです。定期的なメンテナンスを怠ると、加工精度が低下したり、故障の原因となったりする可能性があります。
導入前に検討すべき他の加工方法との比較
ウォータージェット加工以外にも、レーザー加工機やプラズマ切断機など、様々な加工方法があります。各加工方法の得意な材料と不得意な材料やコスト、求める生産量や品質要件を考慮し、加工対象となる材料に最適な加工方法を選定することが重要です。
実際に加工できるかのテスト
導入を検討する際には、実際に加工材料でのサンプルテストを行うことをお勧めします。求める加工精度が得られるか、必要な生産量を処理できる能力があるかなどを確認しましょう。
北川鉄工所では、導入前のサンプル加工テストを承っておりますので、実際の加工結果をご確認いただけます。まずはお気軽にこちらからお問い合わせください。
キタガワのラインナップ
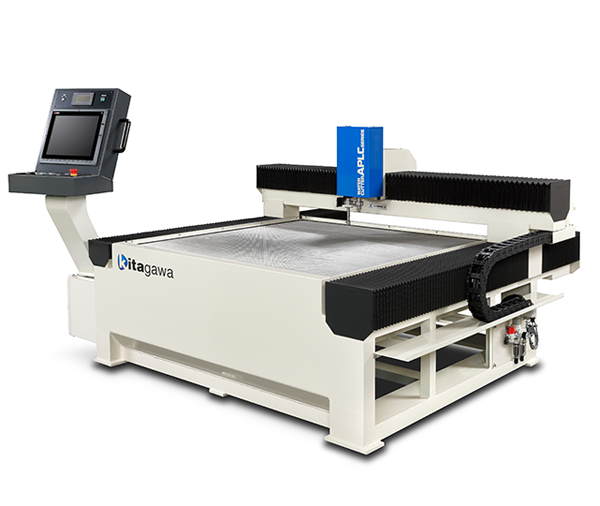
低価格モデル
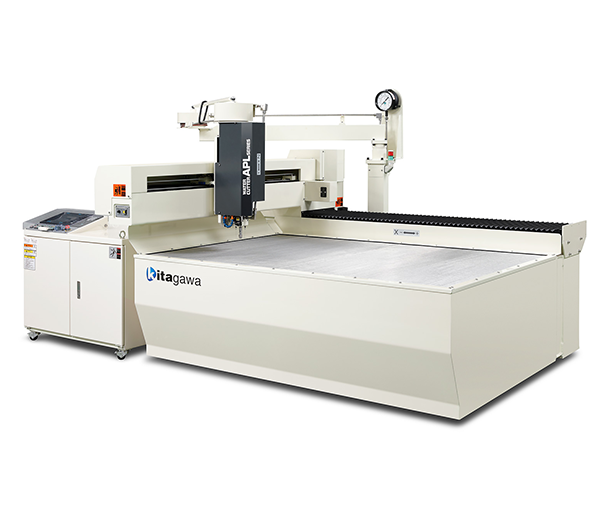
2軸制御ウォーターカッター
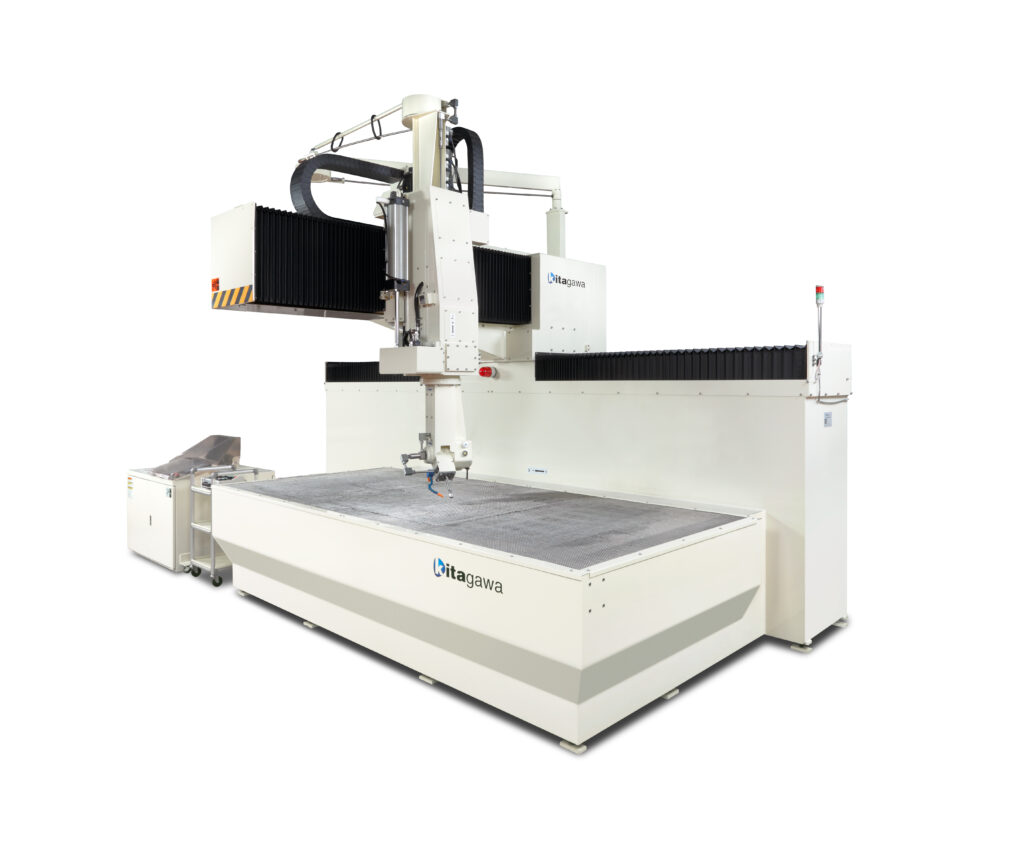
5軸制御ウォーターカッター
北川鉄工所では、コストパフォーマンスに優れたモデルからハイエンドの高精度モデルまで幅広く取り揃えています。お客様の加工ニーズや予算に合わせて、最適な機種を選定可能です。お客様の生産性向上に貢献する最適なソリューションを提供いたします。
詳しい製品情報は、こちらからご確認ください。
巻き癖除去装置
長期間ロール状で保管されたジョイントシ-トは、巻き癖がついてしまい加工精度に影響を与える可能性があります。巻き癖除去装置は、材料を装置に取り付け、適切な圧力をかけながら自動送りすることで、簡単に巻き癖を除去する装置です。
癖取り後の材料は、ウォーターカッターでの加工はもちろん、カッティングプロッターやプレス加工など、さまざまな用途にご使用いただけます。
巻き癖除去装置については、こちらをご確認ください。
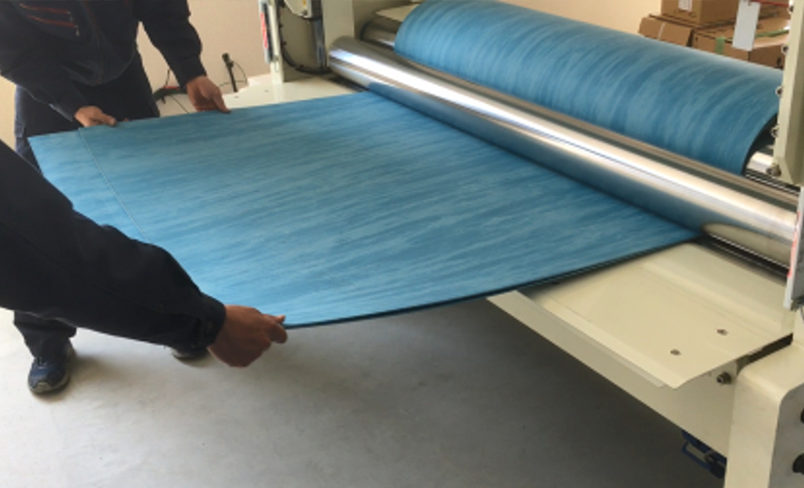
ウォーターカッターの導入は北川鉄工所にお任せください。
北川鉄工所は、工作機械メーカーとして培った技術とノウハウを活かし、お客様のニーズに最適なウォータージェット加工機をご提案いたします。導入前の実証テストから、設備の選定、設置工事、アフターサービスまで、一貫したサポート体制でお客様の生産性向上をバックアップします。
まずは以下のリンクから、お気軽にご相談ください。
・各種お問い合わせフォームはこちら
・テスト加工依頼はこちら
・資料ダウンロードはこちら