摩擦圧接の原理と設備紹介(他の接合方法との比較もあり)
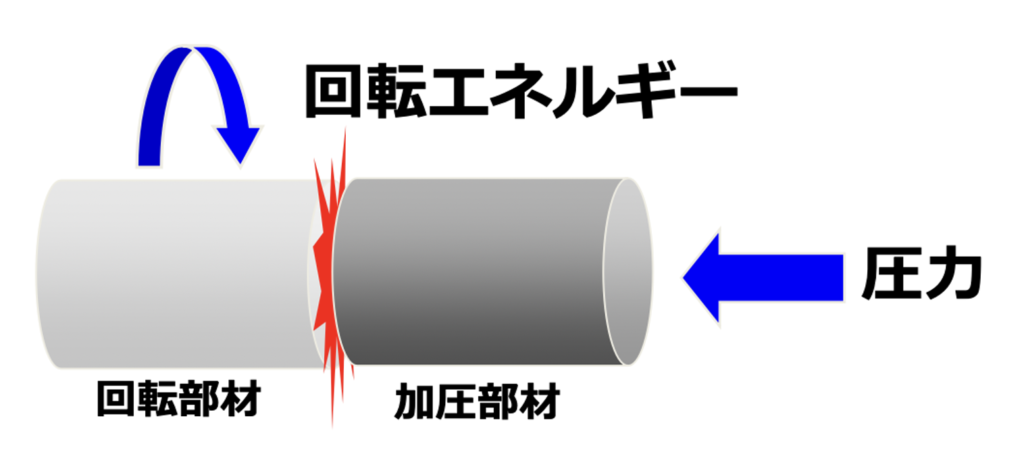
異素材の接合
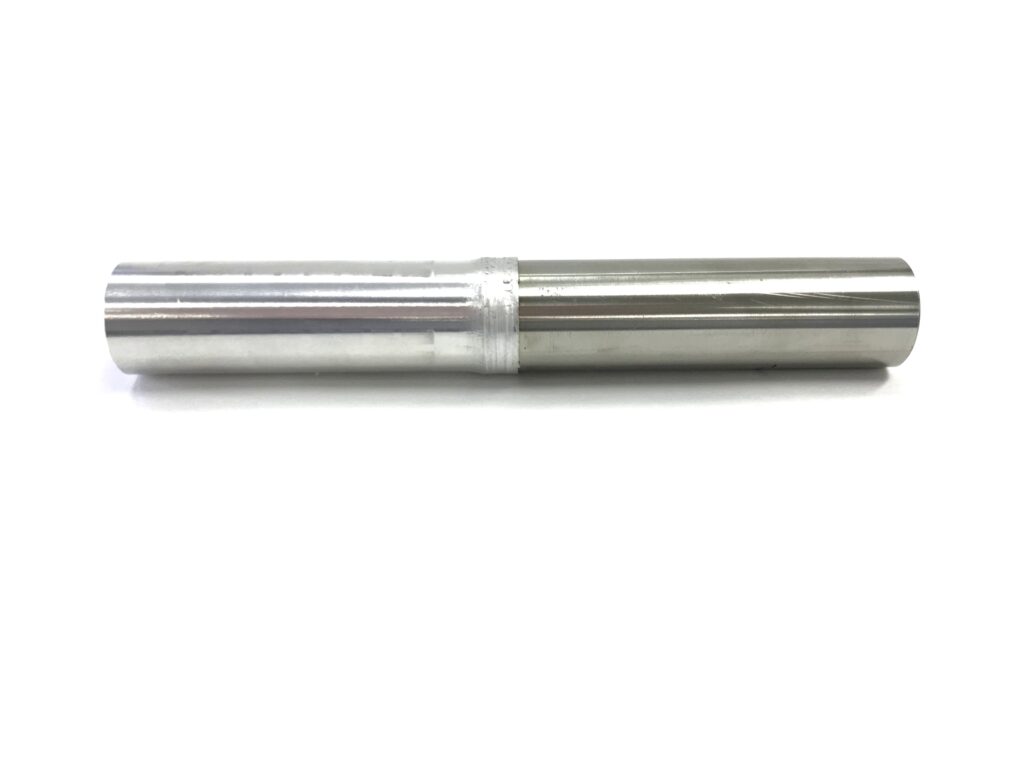
中空化による軽量化
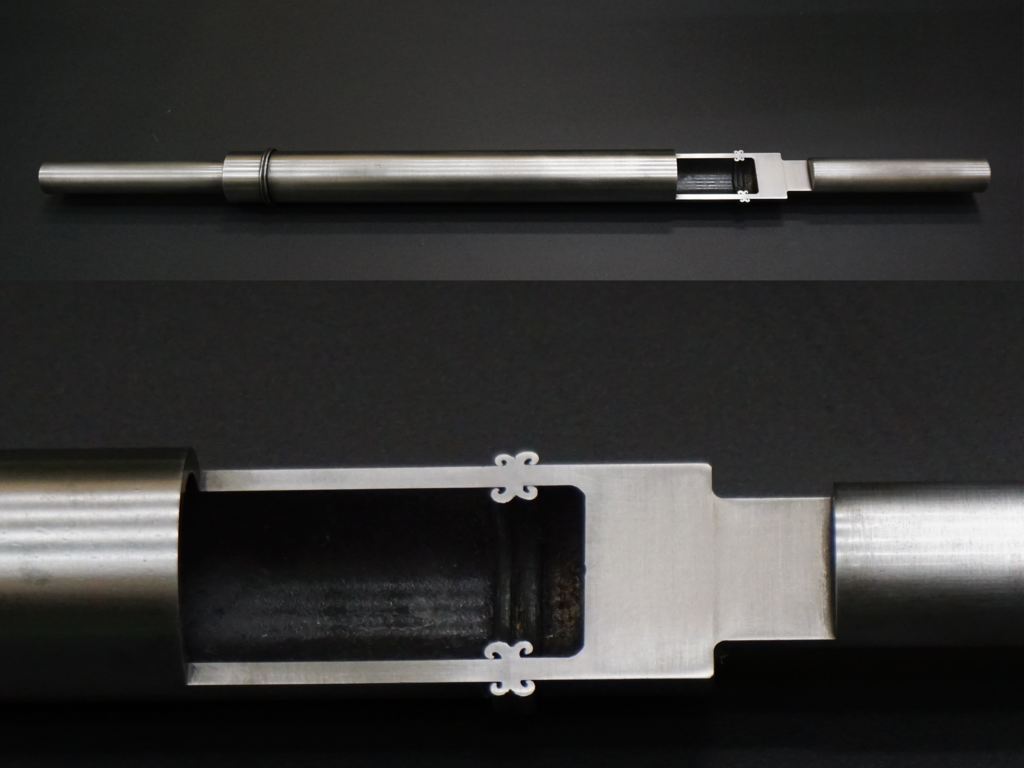
強固な溶接
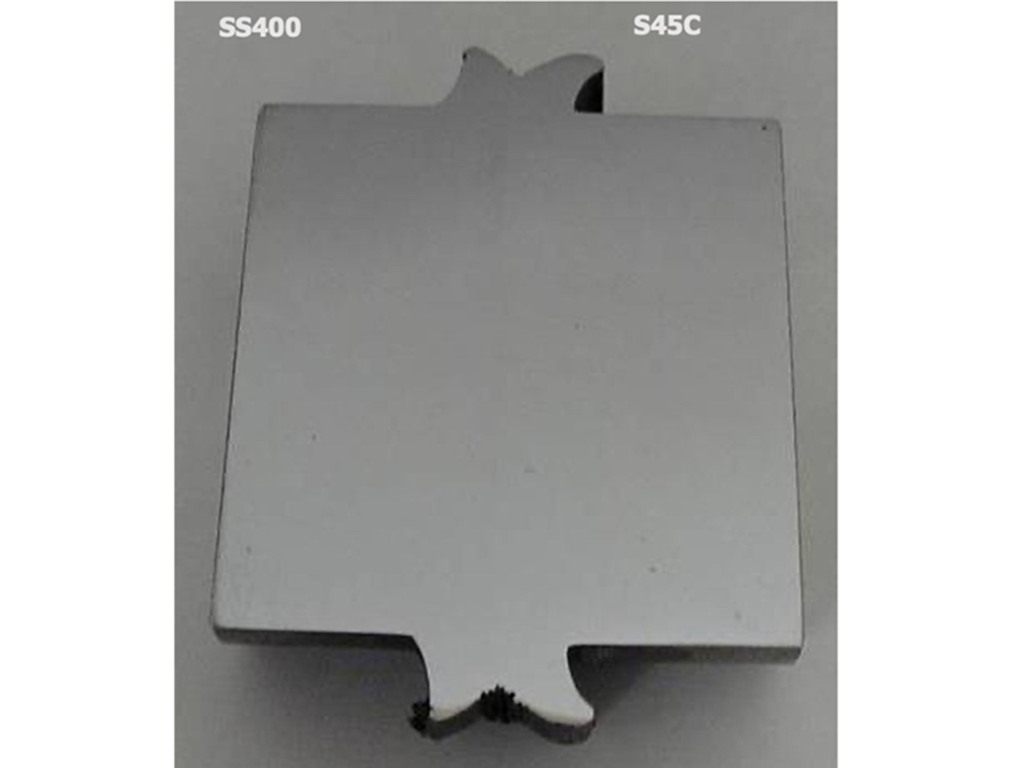
製造業における部品接合は、製品の性能と品質を大きく左右する重要な工程です。
中でも「摩擦圧接」は、他の接合方法にはない高い強度と精度を両立する技術として様々な分野で活用されています。本記事では、摩擦圧接の原理から、他の接合方法との違いまで解説します。
北川鉄工所について
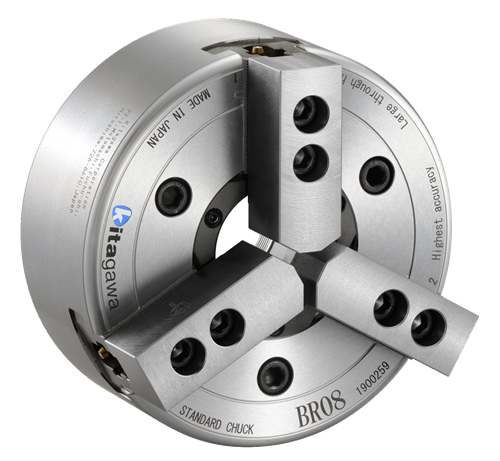
北川鉄工所は、工作機械用チャックにおいて国内シェア60%を誇る産業機器メーカーです。1918年の創業以来、100年以上にわたり日本のものづくりを支え続けてきました。
当社の事業は、金属素形材部門、工作機器部門、産業機械部門の3つを柱としており、世界中の製造業に向けて高品質な製品を提供しています。
摩擦圧接機においては、チャック製造で培った高度な技術力を活かし、高精度で信頼性の高い製品を開発・製造。特に、独自のセンタードライブ方式を採用した2面摩擦圧接機は業界でも高い評価を得ています。
お客様のご要望に合わせたカスタマイズ製品の提供を得意としており、設計から導入後のサポートまで一貫したサービスを提供しています。
詳しい製品情報については、製品一覧をご覧ください。
摩擦圧接とは
摩擦圧接は、2つの部材を高速回転させ、そのときに発生する摩擦熱で接合する技術です。
この工法の特長は、溶接のような溶加材を使用せず、母材同士を直接接合できることです。異種材料の接合も可能で、自動車部品や建設機械、船舶部品など幅広い産業分野で活用されています。
さらに、摩擦圧接は作業環境の改善にも貢献できる加工方法です。溶接と異なり、スパッタ(飛散する金属粒子)の発生が少なく、有害なヒュームも発生しません。加えて、熟練工の技能に頼ることなく安定した品質が得られ、自動化にも適しています。
動画で見る摩擦圧接の仕組み
摩擦圧接の原理について
摩擦圧接は、高速回転と加圧による摩擦熱を利用して金属同士を接合する技術で、面全体を接合するため非常に強度の高い接合が可能になります。
一方の部材を高速で回転させながら、もう一方の部材に強い圧力を加えることで、接合面が摩擦により発熱。炭素鋼の場合、約1100℃~1200℃まで温度が上昇し、塑性変形を起こします。その後、回転を停止し、さらに強い圧力を加えることで、材料は固化し、接合部の結合分子がファンデルワールス力によって高い結合力を発揮します。この過程で、接合面は母材と同等以上の強度を持つ一体構造となります。この強固な結合は、溶接のような溶融状態を経ないため、熱影響層が小さく、母材の特性を損なわずに接合できる点が大きな利点です。
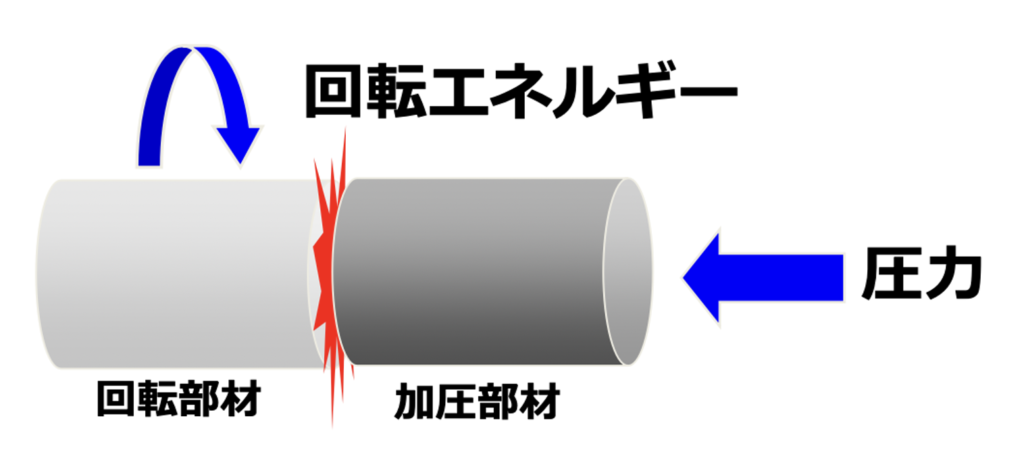
摩擦圧接とその他の接合加工の違いについて
接合加工の方法には様々な方法があります。
ここでは、代表的な接合加工の方法として、溶接、ろう付け、接着剤を用いた接合と、摩擦圧接の違いを比較してみましょう。
溶接は母材を溶融させて接合するため、熱影響による母材の変質や歪みが発生します。
ろう付けは、母材の融点より低い温度で溶ける金属(ろう)を用いるため、接合強度が摩擦圧接より低い傾向があります。
接着剤を用いた接合は、高い精度が求められる用途には不向きです。
一方、摩擦圧接は、高温による母材の変質が少なく、高い接合強度と精度を両立できる点が大きな特徴です。また、溶接のようにスパッタの発生も少ないため、クリーンな作業環境を維持できます。これらの特性から、摩擦圧接は、高い精度と高い強度が求められる様々な産業分野で活用されています。
摩擦圧接の断面と接合強度
摩擦圧接は、接合面全体が均一に接合されます。摩擦熱と圧力によって接合面全体が均一に塑性流動を起こし、原子レベルで結合するため、部分的な未接合や欠陥が少ないという特徴があります。
また、摩擦圧接では、摩擦熱と圧力によって組織が微細化され、緻密になります。母材同士が一体化したような状態になり、接合界面という明確な境界線が見られません。
摩擦圧接は、適切な条件で接合された場合、母材と同等以上の強度を示します。引張試験を行うと、多くの場合、破断は接合部ではなく母材部で発生します。これは、接合界面での結合力が母材の強度を上回っていることを示しています。
硬度分布を測定すると、接合界面で硬度が上昇していることがわかります。これは塑性変形による結晶粒の微細化が原因です。
摩擦圧接の接合可能材質について
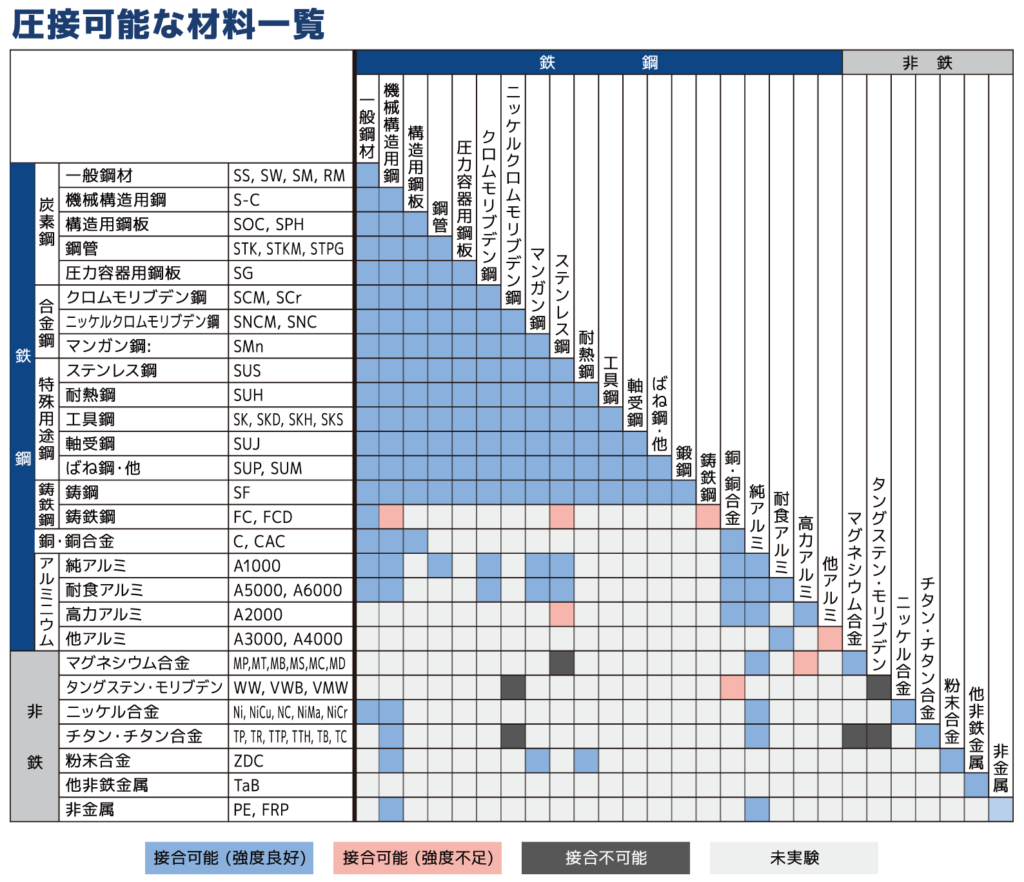
出典元:一般社団法人摩擦接合技術協会
S35C + SUS304
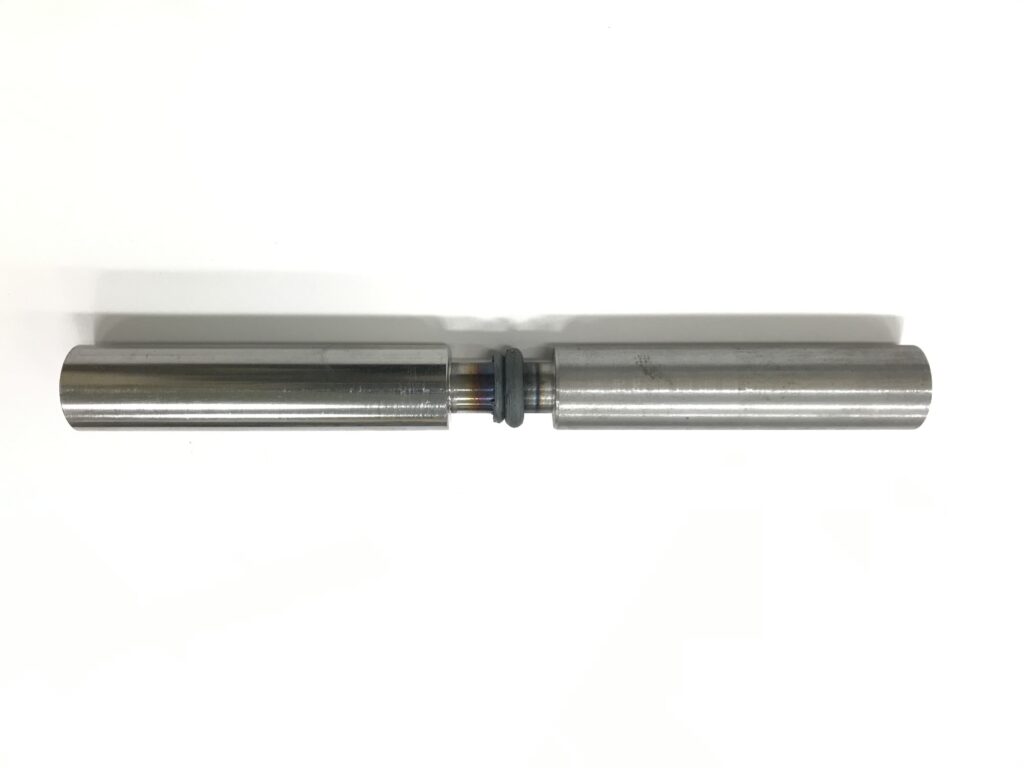
アルミ合金+ステンレス
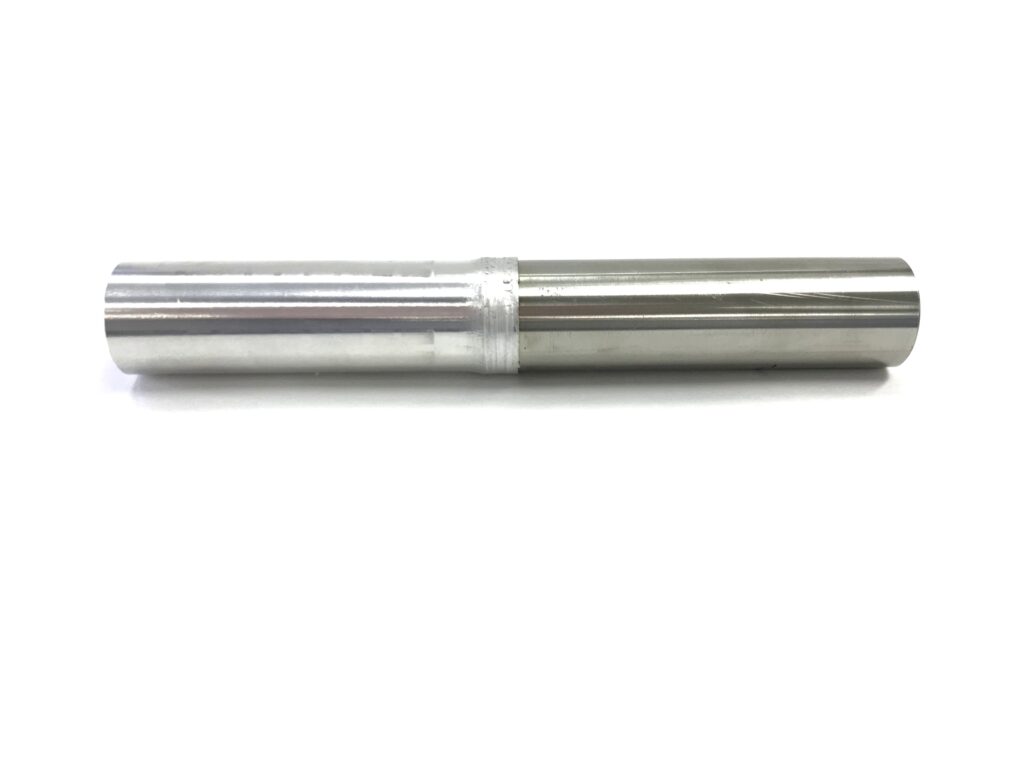
S45C + SD390

弊社NC円テーブル部品
高力黄銅 + S45C
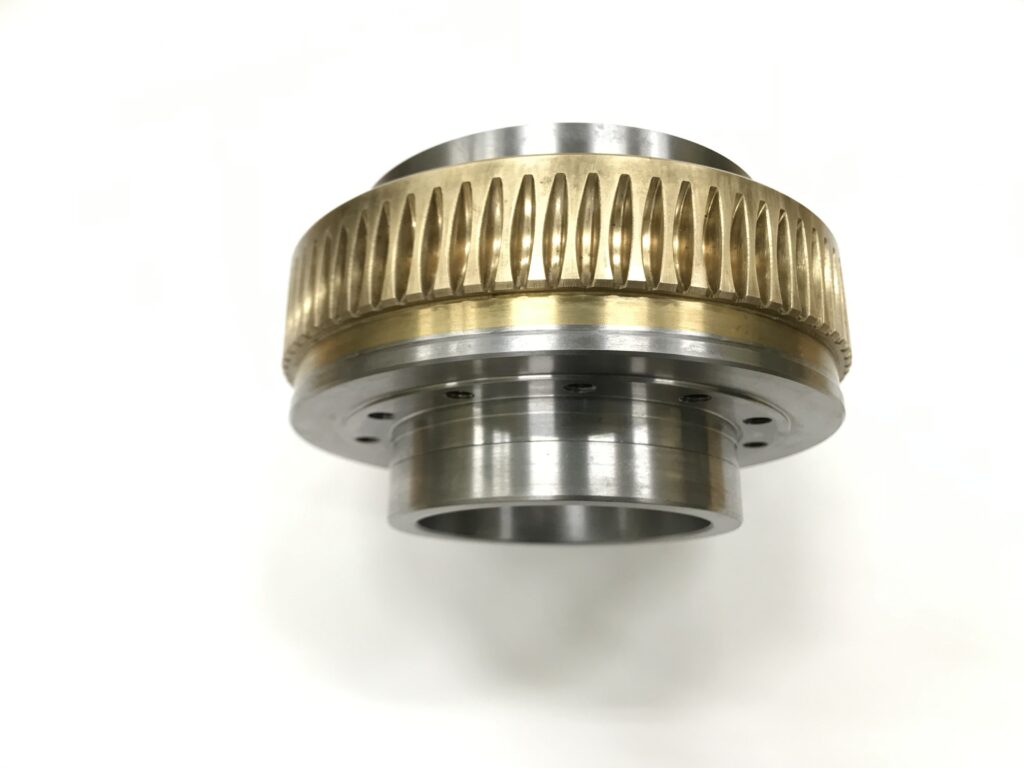
摩擦発熱時間と負荷圧力を制御することで、融点の異なる材料も接合することが可能です。
溶接では困難な材料同士も、圧接工法により選択肢を広げることができます。
摩擦圧接がよく使われる場面と部品
摩擦圧接がよく使われる場面と部品摩擦圧接は、その優れた接合強度と品質から、様々な産業分野で広く活用されています。特に、強度や信頼性が求められる部品や、異種金属の接合が必要な場面で重宝されています。
自動車産業
高い強度と耐久性が求められる部品に用いられます。摩擦圧接は、異種金属(例えば、鋼とアルミニウム)の接合にも適しており、軽量化にも貢献できます。
摩擦圧接が使われる部品例
ドライブシャフト、ステアリングシャフト、アクスル、ピストンロッド
航空産業
航空機は極めて高い安全性と信頼性が求められます。航空機は様々な気象条件にさらされるため、使われる部品は対候性や耐食性も必要です。
摩擦圧接が使われる部品例
ジェットエンジン部品、プロペラシャフト、アジャスターレバー
鉄道車両
鉄道車両は、走行中に繰り返し荷重を受けるため、使われる部品は高い疲労強度が求められます。
摩擦圧接が使われる部品例
車軸、連結器
建設機械
建設機器は過酷な環境で使用されるため、高い耐久性、強度、そして安全性が求められます。
摩擦圧接が使われる部品例
油圧シリンダー、アーム、ローラ
その他
ポンプシャフト、建築構造物、プラント設備
摩擦圧接のメリットとデメリット
摩擦圧接は、以下のようなメリットがあります。
摩擦圧接のメリット
高品質な接合
- 母材同等以上の接合強度を実現
- 異種金属の接合が可能
- 溶接に比べて熱影響が少なく、変形が小さい
- 接合部全体が均一に接合される
- 位置決め精度が高く、高精度な接合が可能
- 内部欠陥が少ない高品質な接合部
- スパッタやヒュームの発生が少なく、作業環境が良好
高い生産性
- 自動化が容易で安定した品質が得られる
- 熟練工の技能に依存しない
- 短時間での接合が可能
- 溶加材が不要でコスト削減に貢献
摩擦圧接のデメリット
多くのメリットがある一方で、デメリットもあります。
形状の制約
- 基本的に円形断面の部材が対象
- 異形材の接合には特殊な治具が必要
- 極端な薄肉材や細径材は接合が困難
設備面の課題
- 専用の摩擦圧接機が必要で初期投資が高額
- 部材に応じた治具の準備が必要
- 設置スペースの確保が必要
技術面の課題
- 接合条件の最適化に経験とノウハウが必要
- 材質の組み合わせによっては接合が困難
- 接合後のバリ取りなど後工程が必要
キタガワの摩擦圧接について
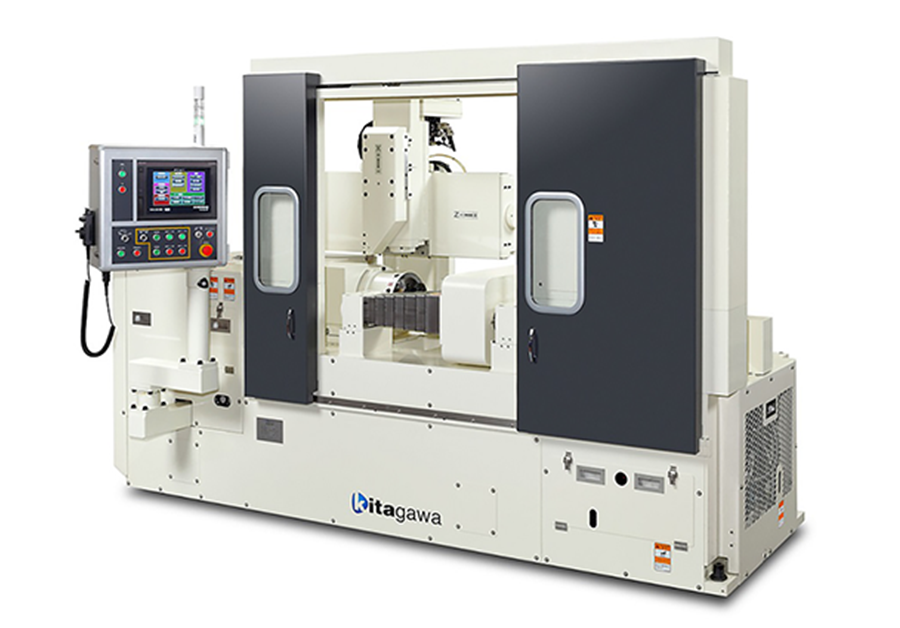
摩擦圧接機
キタガワのチャック技術を活用した摩擦圧接機です。お客様のニーズに合わせた製品づくりをコンセプトとしており、使い勝手にこだわったカスタマイズ品をご提供いたします。
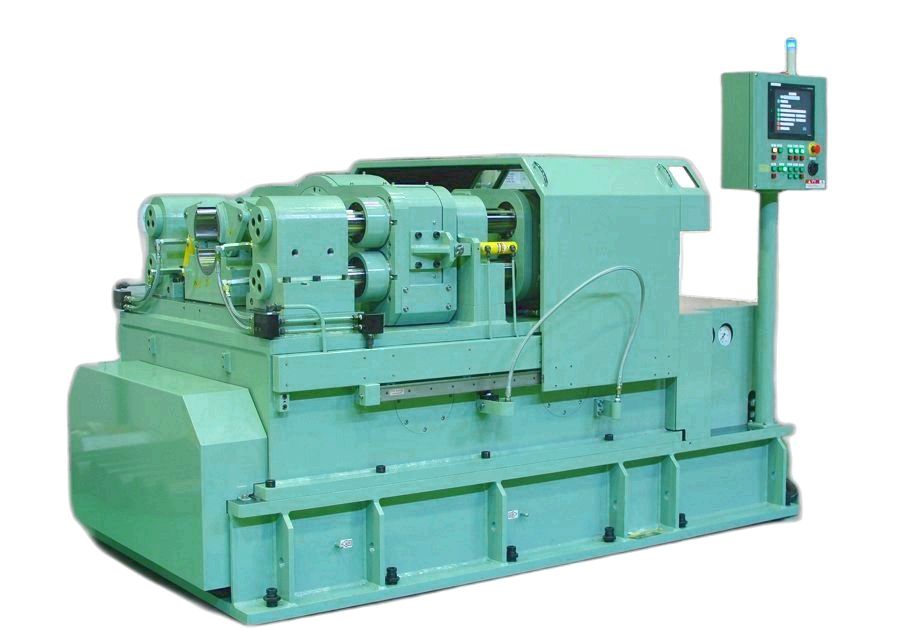
2面摩擦圧接機
独自技術の『センタードライブ方式』を採用した、2面同時摩擦圧接機です。位相制御、長尺品、異形材の接合を得意としており、サイクルタイム短縮にも貢献出来ます。
北川鉄工所は、チャック製造で培った高度な技術力を活かし、高精度で信頼性の高い摩擦圧接機を提供しています。特に、独自のセンタードライブ方式を採用した2面摩擦圧接機は、業界でも高い評価を得ています。
当社の摩擦圧接機は、1面圧接機と2面圧接機の2種類をラインナップ。1面圧接機は、汎用性が高く幅広い接合に対応可能です。2面圧接機は、独自開発のセンタードライブ方式により、2面を同時に高精度で接合できる特長があります。
お客様のニーズに合わせた幅広いカスタマイズにも対応。チャック部品の選定から、装置の仕様変更、自動化対応まで、お客様の生産環境に最適な摩擦圧接機を提供いたします。導入前のテスト加工から、設置、アフターサポートまで、一貫したサービスでお客様の生産性向上をサポートいたします。
設備のカスタマイズ事例はこちら
摩擦圧接の設備導入は北川鉄工所にお任せください
100年以上の歴史を誇る北川鉄工所の摩擦圧接機は、チャック製造で培った高度な技術力と豊富なカスタマイズ実績により、お客様の生産現場に最適なソリューションを提供します。
まずは以下のリンクから、お気軽にご相談ください。
・各種お問い合わせフォームはこちら
・テスト加工依頼はこちら
・資料ダウンロードはこちら